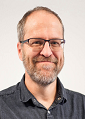
Dr Neil Fellows
Dr Neil Fellows is a Reader in the Engineering in the School of Engineering, Computing
Title: Residual stress prediction in metal matrix composites using curvature
Biography
Biography: Dr Neil Fellows
Abstract
Metal matrix composite (MMC) materials can provide very desirable material and component properties. MMCs can be divided into those that are reinforced by long continuous fibres (such as carbon, alumina, silicon, boron and carbide) or those reinforced by discontinuous fibres (particulates). The addition of fibres and particulates enables the property of the base metal (matrix) to be enhanced. The strength properties of MMC’s are known to be heavily influenced by the manufacturing process, caused by changes in the matrix microstructure and through the introduction of residual stresses. It is very difficult to measure the residual stresses within MMCs which leads to uncertainty in terms of the prediction of those stresses. To overcome these issues an indirect method to predict the residual stresses, through matching numerical and experimental curvature, is presented in this paper. The MMC chosen for investigation is Aluminium 6061 reinforced with silicon carbide long fibres. The numerical models presented are for an aluminium plate with internal layers of silicon fibre that have been arranged in 0°/90° or +55°/-55° directions, such that the plates are non-symmetrical about the midline. The numerical models take into account the material property changes due to creep and thermal loading. To test the numerical models ability to predict curvature, aluminium plates were manufactured to the same specifications using the same manufacturing process conditions as used in the models. The curvatures between the models and manufactured plates showed good correlation, giving confidence in the models ability to predict the residual stresses for more complex components